Discover the benefits of plastic extrusion in product development
Discover the benefits of plastic extrusion in product development
Blog Article
Understanding the Basics and Applications of Plastic Extrusion in Modern Production
In the realm of modern-day production, the technique of plastic extrusion plays an instrumental role. Untangling the principles of this procedure discloses the real adaptability and possibility of plastic extrusion.
The Principles of Plastic Extrusion Refine
While it may appear complex, the basics of the plastic extrusion process are based upon reasonably straightforward principles. It is a manufacturing process where plastic is melted and after that shaped into a continuous profile via a die. The raw plastic product, usually in the kind of pellets, is fed right into an extruder. Inside the extruder, the plastic undergoes warm and stress, triggering it to thaw. The molten plastic is then required through a shaped opening, called a die, to form a long, continuous product. The extruded product is cooled and afterwards cut to the wanted length. The plastic extrusion procedure is thoroughly made use of in different industries because of its performance, cost-effectiveness, and flexibility.
Different Kinds of Plastic Extrusion Strategies
Building upon the standard understanding of the plastic extrusion process, it is required to explore the different techniques associated with this manufacturing technique. Both main techniques are profile extrusion and sheet extrusion. In profile extrusion, plastic is thawed and created into a constant profile, typically utilized to create pipelines, rods, rails, and window structures. In contrast, sheet extrusion produces huge, flat sheets of plastic, which are typically more processed into items such as food product packaging, shower curtains, and auto parts. Each strategy requires specialized equipment and precise control over temperature and stress to guarantee the plastic preserves its shape during cooling. Comprehending these methods is crucial to using plastic extrusion successfully in contemporary manufacturing.

The Duty of Plastic Extrusion in the Automotive Sector
A frustrating majority of parts in contemporary vehicles are items of the plastic extrusion process. This process has changed the auto industry, changing it into an extra efficient, cost-effective, and versatile manufacturing field. Plastic extrusion is mostly used in the manufacturing of various auto elements such as bumpers, grills, door panels, and dashboard trim. The process provides an attire, constant outcome, making it possible for manufacturers to create high-volume get rid of great accuracy and very little waste. The lightness of the extruded plastic components adds to the general decrease in car weight, improving gas performance. The resilience and resistance of these parts to warm, cool, and impact enhance the long life of autos. Thus, plastic extrusion plays a critical function in auto manufacturing.
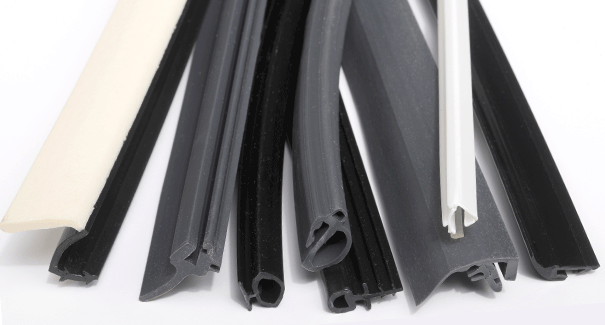
Applications of Plastic Extrusion in Durable Goods Manufacturing
Past its considerable effect on the automotive market, plastic extrusion verifies similarly effective in the realm of consumer products producing. This process is vital in producing a wide selection of products, from food packaging to family devices, playthings, and even medical devices. The flexibility of plastic extrusion allows makers to create and create intricate sizes and shapes with high accuracy and effectiveness. Due to the recyclability of numerous plastics, squeezed out elements can be reprocessed, reducing waste and expense (plastic extrusion). The versatility, adaptability, and cost-effectiveness of plastic extrusion make it a recommended selection for several durable goods manufacturers, contributing substantially to the sector's growth and development. The environmental implications of this prevalent usage require careful consideration, a topic to be discussed better in the subsequent area.
Ecological Effect and Sustainability in Plastic Extrusion
The prevalent usage of plastic additional info extrusion in producing invites analysis of its eco-friendly ramifications. Effective machinery his response minimizes energy use, while waste administration systems recycle scrap plastic, lowering raw material demands. Regardless of these enhancements, additionally technology is needed to mitigate the ecological impact of plastic extrusion.
Conclusion
In conclusion, plastic extrusion plays a crucial duty in modern production, especially in the automobile and customer goods industries. Comprehending the basics of this process is key to optimizing its applications and advantages.

The plastic extrusion procedure is visit this page thoroughly made use of in various markets due to its performance, cost-effectiveness, and convenience.
Building upon the standard understanding of the plastic extrusion procedure, it is needed to discover the numerous methods involved in this production technique. plastic extrusion. In contrast, sheet extrusion creates huge, flat sheets of plastic, which are normally further processed into items such as food packaging, shower drapes, and automobile parts.A frustrating bulk of parts in contemporary vehicles are products of the plastic extrusion procedure
Report this page